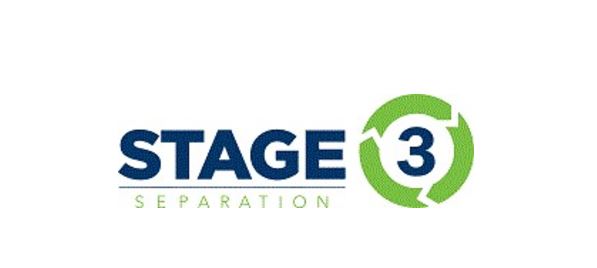
Job Title: Solids Control Field Technician Trainee Grade: 00 Company/Department: Operations Reports To: Field Leader Position Duration: ~2-6 months FLSA Status: Non-Exempt Pay: Company Vehicle: Not Eligible Hours: Monday through Sunday 12:00 AM – 12:00 PM / 12:00 PM – 12:00 AM 30-minute break (unpaid). General Description: The Solids Control Field Technician – Trainee (FTT), works Under general direction from and reporting to the Field Leader(s). FTT’s are responsible for learning the mechanical processes which are used to provide enhanced drilling operations and recycle drilling fluid through closed loop and other mud systems. FTT’s will observe and job shadow daily rig operations by learning and mentoring under a Field Leader(s) and Technician. |
ESSENTIAL FUNCTIONS: Able to work 14 days on and 7 days off, or 20 days on 11 days off. (Schedule will vary by Basin). Able to work 12-hour shifts (rotation), daily, including overtime. Able to work a Swing (rotation) from 12:00PM to 12:00AM or 12:00AM to 12:00PM. Trainee will job shadow with an experienced Technician and Field Leader. Must be able to travel domestically to remote rig locations, in personal vehicle, throughout the United States. Will be assigned to one rig for rotation, or multiple rigs – based on business requirement. Will learn how to rig up and rig down equipment. Will learn and operate a variety of solids control equipment including shaker tanks, centrifuge, drying equipment, and pumps. Will develop basic understanding of oil and gas drilling processes. Will develop basic knowledge of Environmental Services. Will gain an understanding of basic electrical principles. Will develop an understanding of drilling fluid properties including drilling fluid weight, funnel viscosity, retort analysis, etc., and will perform drilling fluid analysis. Will learn how to perform various solids control services such as air drilling, barite recovery, de-watering, floc water, fluid transfers, target lo gravity solids, cuttings drying/invert recovery, etc. Will learn how to perform basic routine maintenance services and routine electrical services on various equipment. Will learn how to move cuttings from pits to trailers, by operating heavy machinery, safely and efficiently, with supervision. Must maintain a clean and orderly “backyard” by using a variety of pressure washing equipment. Will attend and actively participate in daily safety meetings. You will be responsible for completing daily PJRA/JSA, inspection reports, observation reports, and checklists, as required. You will be required to wear proper PPE/FR’s while working in the backyard of a drilling rig. Must always abide by safety protocols. |
Required Knowledge, Skills, and Abilities: Team player who can work independently. Must be mechanically inclined with comprehension for electronics. Will learn how to input routine data into various systems including company Portal. Must be a problem solver and use time efficiently. Must have ability to develop professional relationships with everyone working on the rig. Must be customer service oriented, learning how to use diplomacy and tact. Will learn how to operate and will operate an excavator, forklift or Wheel Loader and will operate them daily, will and earn certification. Will earn certifications for various Rig Safety programs including PEC Safe Land, H2S, and CPR/First Aid. Must be able to work outdoors in all weather conditions (cold, wet, and hot). Must have the ability to be away from home for 14 days or longer, to complete scheduled rotation (hitch). Must keep living quarters clean, and orderly. Must be able to read, write and comprehend English. Trainee will advance to Field Level 1 by passing a Performance Evaluation and competency test(s). |
Minimum Required Education, Credentials, Licenses and Experience: High School diploma, or GED equivalent. 2-year Associate’s degree or technical diploma, in Technology, Electronics, or Mechanics, or similar field, is preferred. Prior Forklift, Excavator, or Wheel Loader experience, or Certifications, is/are preferred. Certification training will be provided prior to working on a rig. Basic Microsoft Office experience including Outlook. Must have a valid State driver’s license, valid insurance, and an acceptable driving record.Must have reliable transportation to and from assigned rig site locations.Must be able to pass a Pre-employment; Fit for duty test, drug test (urine and hair follicle), background evaluation and have an acceptable Motor Vehicle Review. |
Supervisory Level: Check the type of supervision received that best fits the position: ☒ Close Supervision: Work is reviewed at several steps along the way for accuracy. (Generally, pertains to entry level or trainee positions.) ☐ Supervision: Incumbent performs standard and routine assignments independently to conclusion; unusual problems which may require exceptions to procedures or processes are referred to the supervisor. (Generally, applies to “journey level” worker able to work independently.) ☐ General Supervision: Incumbent develops procedures for performance of a variety of duties or performs complex duties within established policy guidelines; responsible for a defined set of assignments, e.g., all financial activities for the department; is expected to determine and create necessary procedures to set priorities and meet specific goals and objectives of the function or unit. (Typically pertains to advanced/operational, senior professional, unit supervisor) ☐ Direction: Establishes procedures for attaining specific goals and objectives in a broad area of work. Only final results are reviewed. (Typically applies to a manager or expert/top level professional.) ☐ General Direction: Receives guidance in terms of broad goals and overall objectives and establishes the methods to attain them. Generally, the incumbent oversees an area of work and typically formulates policy for this area but does not necessarily have final authority for approving policy. |
Work Environment: Identify the working conditions which relate to the essential functions of the position, such as working indoors/outdoors, working with exposures to hazards, etc. Include special considerations for the position, such as occasional travel or necessary overtime. Choose All that Apply: ☒ 12:00/12:00 work schedule ☒ Shifts over 12 hours typical ☒ Travel (100%) ☒ Toxic or caustic chemicals ☐ Explosives ☐ Radioactive materials ☐ Not substantially exposed to adverse environmental conditions (as in typical office or administrative work). ☐ Inside environmental conditions: Protection from weather conditions but not necessarily from temperature changes. ☒ Outside environmental conditions: No effective protection from weather. ☒ Both environmental conditions: Activities occur inside and outside. ☒ Extreme cold or heat: Temperatures typically below 32 degrees for periods of on hour or above 100 degrees ☒ Noise: There is sufficient noise to cause the worker to shout in order to be heard above the ambient noise level. ☒ Hazards: Includes a variety of physical conditions, such as proximity to moving mechanical parts, moving vehicles, electrical current, working on scaffolding and high places, exposure to high heat or exposure to chemicals ☒ Atmospheric conditions: One or more of the following conditions that affect the respiratory system of the skin: Fumes, odors, dusts, mists, gases or poor ventilation. ☐ Confined space entry ☐ OTHER: Physical Demands: These physical demands are representative of the physical requirements necessary for an employee to successfully perform the essential functions. Reasonable accommodation can be made to enable people with disabilities to perform the described essential functions of the job.___________________________________________________________________________________________ |